C_TS413_2020 – SAP Certified Application Associate Interview Questions
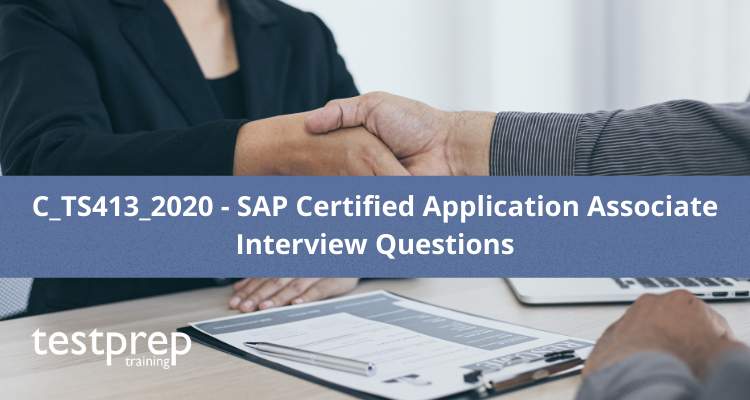
Exam and interview preparation are both necessary. As a result, interview preparation takes far more time, effort, and confidence than studying for an exam. Make the most of your one and only chance to make a good first impression. As a result, we’ve done our best to provide you with the most current and expert-reviewed interview questions to assist you in preparing for the C_TS413_2020 – SAP Certified Application Associate exam. From basic to sophisticated, we’ve covered all of the C_TS413_2020 – SAP Certified Application Associate Interview Questions. As a result, in order to optimize their chances of success, we strongly advise applicants to prepare to the best of their abilities.
The following are some of the most frequently asked C_TS413_2020 – SAP Certified Application Associate interview questions. As a result of having a greater understanding of the sorts and patterns to expect, candidates will be better prepare.
1. What is a warehouse’s inbound process?
Items that arrive at the warehouse via external sources or from another corporate site start the flow of commodities into the warehouse. To get items through reception and into storage, warehouse tasks are undertaken at various levels of complexity.
2. What is the VAS order’s purpose?
A value-added service (VAS) is a form of customer service that adds value to the client’s experience beyond the essential services that are already available, such as transportation, delivery, and warehousing. VAS orders specify that VAS be perform on one or more products, as well as that delivery items be link to the packing instructions.
3. What is the definition of deconsolidation?
You can associate a single handling unit with several putaway handling units using the deconsolidation function. When different items in a de-consolidate handling unit need to be store in different storage spaces, this is necessary.
4. Could you clarify how the SAP system handles cross-docking? What is the purpose of cross-docking?
Cross-docking reduces the time it takes to deliver an item to a client by allowing goods to be transferred between locations inside a warehouse in one step. It can only be utilised when the stock-in and stock-out locations are not establish by the first-in, first-out principle (FIFO).
5. Do you have any experience with SAP wave management?
Extended Warehouse Management can be used to group or separate outbound delivery goods from warehouse requests into waves. These waves must be collect and processed at the same time so that each wave’s items can be shipped at the same time.
6. What is the SAP kitting process in C_TS413_2020 ?
Kitting is a procedure in which components are gathered together and package as a kit in the manufacturing industry. Kitting is commonly use to reduce time by lowering the amount of time it takes to locate products in inventory. The pre-assembled parts are then transported to the location of use. Kitting is a warehouse management assembly process in which raw, semi-finished, and finished materials are assembled into final products.
7. In C_TS413_2020, how would you define staging?
By staging manufacturing materials in SAP Production and Distribute Materials, you can build a production order in the system. Based on the quantity of units required, the EWM system generates a production material request (PMR) for the manufacturing order.
8. What are the benefits of using SAP for labor management?
Features for successfully scheduling and utilizing resources are offered in the SAP module. The Labor-Management module in SAP allows a warehouse to properly plan, manage, and use resources. Employee performance can be assessed by contrasting planned work with actual work complete.
9. Could you explain how the exception code is used in SAP?
In its Customizing environment, has a test tool for exception code assignment that may be use to ensure that the workflow is properly linked. Start the text tool and select a business context and an execution step for an exception code to test the exception code linkage.
10. In SAP C_TS413_2020, what does the phrase batch mean?
Batch management is a method of tracking individual products as they move through the supply chain. It is a feature of SAP ERP that is part of the logistics section. When individual batch traceability is required, batch management is employ. This could be due to varying quality due to varied manufacturing output, or it could be because the item has expired by the time it arrives at its final destination.
11. What is the SAP serial number?
A serial number is a unique number that combines the material number with the serial number. In SAP, the material number and serial number combination must be unique. In Inventory Management, serial numbers are use to distinguish between individual things and other material products.
12. Which combination necessitates the use of Labor Management?
Number of warehouses and workforce activities
13. What are the five primary components of SAP’s warehouse management system?
- Firstly, number assigned to the warehouse.
- Secondly, type of storage.
- Section for storage.
- Bin for storing items.
- Area of Activity.
14. In a warehouse, what is the highest and smallest unit in C_TS413_2020 ?
Warehouses are organize in a hierarchy, with the warehouse number at the top. One of the smallest units is a Storage Bin. A description of the exact position of all the products in that specific warehouse may be found inside each bin.
15. What exactly are availability checks, and how do they work in SAP?
The following are the three types of availability checks:
- Firstly, depending on the ATP levels, perform a check.
- Secondly, Make certain that the product distribution is accurate.
- Next, In view of the current scenario, consider the idea.
- You can choose whether an availability check is perform against the ATP quantity or the expected quantity in Customizing. The material master, together with the rest of the system, manages the check against product allocations.
16. What role does the sales document type play in the sales process?
Based on the kind of sales document, item type, and item category, the system replicates and restricts advertising sales. The kind of sales document is specified during the development of a sales document.
17. How does the billing process work?
Billing is the last step in the SAP Sales and Distribution module’s business transaction processing. When an order is processed and delivered, billing information is provided at each stage of the order processing process.
18. Could you please define “product allocation” for me?
Product allocation allows products to be distributed at precise times to specific consumers or regions. In Release 3.0F, you can now compare availability to product allocation. For example, if output is low, the first client will not receive the full amount, leading subsequent sales orders to be validate late or not at all.
19. Describe the requirements Class in C_TS413_2020 .
The requirements class contains all parts of planning control, such as relevance for planning, requirements planning strategy, and requirements consumption strategy. Additionally, whether an availability check for the material in the sales and distribution documents should be base on the ATP quantity (ATP = available to promise) and whether needs should be passed on is state at the global level. For sales documents, the schedule line category gives a finer level of control.
20. Give a thorough explanation of the checking rule in C_TS413_2020.
In sales and distribution, the checking rule is use to limit the scope of each transaction’s availability check. You can optionally indicate whether the check’s replenishment lead time should be include or exclude. Individual checking criteria describe which stocks should be examine during the transaction-based availability check, as well as inward and outward commodities movement.
21. Could you give me additional information about the Checking group?
The group in charge of checking determines whether the system should generate individual or group sales and shipment processing needs. For the requirement transfer availability check, you can also design a material block. The checking group can also be use to disable the availability check. When the bill of materials is detonate in the assembly order, this option was create exclusively for the assembly order so that individual components can be mark as non-critical parts for procurement purposes. The checking group and the checking rule establish the scope of the availability check.
22. What are the components of the Check in C_TS413_2020?
A checking rule is assign to each transaction. This rule, in conjunction with the checking group, determines the scope of the availability check. You may determine which of the aforemention elements should be included in the availability check for each transaction using the checking rules in Customizing for Sales.
Include scheduled or production orders, for example, in the availability check for-trade items makes no sense. These orders should, however, be include in the check if your organization manufactures the products. For transactions that generate special stock, such as make-to-order manufacturing, consignment, or returnable packing operations, the availability check is perform against the special stock.
23. Explain the Transportation Unit’s Appointment.
A Transportation Unit (TU) Appointment is a long-term object that holds a reservation for a certain physical transportation unit. To begin, the TU appointment has a number of different statuses (such as checked-in, loading began, and so on) as well as actions that can be perform on it (post-check-in, etc.). The TU position is for planning and implementing yard processes. TU appointments are divided into four categories: planned, active, execute, and invalidate. Each physical TU resource can only have one TU appointment with the state: active (when the physical vehicle actually is in the yard).
24. What factors are taken into account while deciding on a pricing strategy?
The Sales Area (Sales Organization + Distribution Center + Division) + Customer Price Procedure + Document Pricing Procedure establish the pricing mechanism in SD. The Sales Area is provided at the Header Level of the Sales Order. The Customer Pricing Procedure starts with the Customer Master. The Document Pricing Procedure is determined by the Sales Document Type / Billing Type (if configured). When the pricing procedure has been determine, condition records are retrieved.
25. What is the outbound delivery method?
Outbound delivery procedure begins with an outward delivery request and ends with the delivery of products to a product receiver. It combines all outbound delivery-related procedures (triggers for preparation and execution), as well as communication with items received and billing.
26. What part do partner functions play in sales?
In a commercial transaction, use partner functions to specify each business partner’s rights and duties. You assign partner functions when you establish a master record for a business partner.
27. What is Batch Status Management and why do we utilise it?
This component is in charge of determining if a batch is usable or not. For batches that are no longer usable, this allows you to halt the movement of goods, as well as their distribution to customers and use in manufacturing. You can highlight the differences between the two statuses in greater detail by using extra features that you’ve customised to match your needs. As a result, you can define whether a batch was allow or reject for a specific sort of usage.
28. Define the concept of collective processing.
The Collective processing function presents a list of all the transactions you’ve selected based on the criteria you establish on the first screen. This tool makes transaction administration easier by displaying a list of all transactions with common selection criteria and providing the processing capabilities that are require. Move directly from the processing list to the specific transaction for further information. To speed up the selection and processing of all financial transactions, collective processing could be use. To complete all of the essential tasks, you can also use the collective processing technique (such as knock-in or knock-out, exercise, or rollover).
29. What distinguishes Time Deposit – Fast Processing from other deposit options?
You can use the fast-processing option to pick and process fixed-term and notice deposits for several company codes at the same time. Only a few key fields are available for this function. It helps you save time by allowing you to complete the majority of your everyday duties on a single screen. You can also go to the detail screen to make regular entries.
30. Define the Agreement to Manage Scheduling.
The Manage Scheduling Agreement SAP Fiori app allows users to browse and display all scheduling agreements based on the criteria they choose, delve down into the details, and make revisions and follow-up tasks.