C_TS422_1909 – SAP Production Planning and Manufacturing Interview Questions
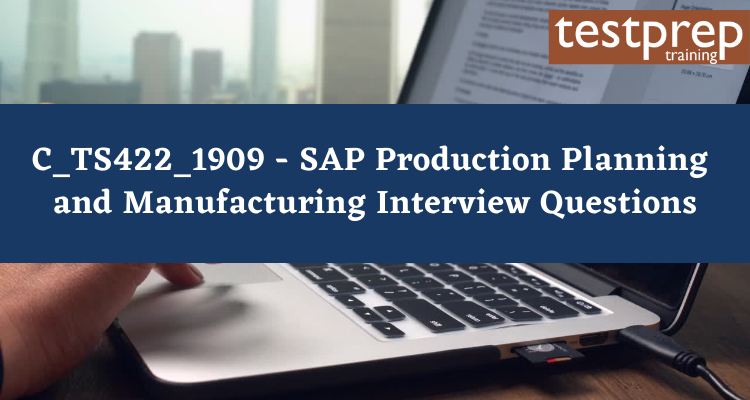
The C_TS422_1909 – SAP Production Planning and Manufacturing demonstrates that the candidate has an overall understanding and in-depth technical skills to participate as a project team member in a mentoring role. It is an associate-level exam that validates a candidate’s fundamental and core knowledge for the SAP S/4HANA Manufacturing consultant profile. Furthermore, be aware that the professional-level certification also necessitates several years of practical on-the-job experience and addresses real-world scenarios. As a result, read the guidelines carefully and follow up for more information. To help you prepare for the C_TS422_1909 – SAP Production Planning and Manufacturing interview we have curated expert level questions and answers:
Advanced Interview Questions
What are the key components of the Bill of Material (BOM) in SAP Production Planning?
The Bill of Material (BOM) in SAP Production Planning is a comprehensive list of all the raw materials, semi-finished products, and components required to manufacture a finished product. The key components of a BOM are:
- Material Number: This is the unique identifier for each item in the BOM. It can be a part number, product code, or any other identifier used to identify the item.
- Quantity: This field specifies the number of units of each item required to manufacture a finished product.
- UoM (Unit of Measurement): This is the unit of measurement used to specify the quantity of each item in the BOM.
- Description: This field provides a brief description of each item in the BOM. This information helps to identify the item and its purpose within the manufacturing process.
- Lead Time: This field specifies the lead time required to receive each item in the BOM. Lead time is the amount of time between the release of an order and the actual delivery of the item.
- Item Category: This field categorizes each item in the BOM into different types, such as raw materials, semi-finished products, finished products, or spare parts.
- Routing: This field specifies the manufacturing process steps required to produce the finished product. It includes information such as the operation sequence, operation time, and resource requirements.
- Costing Information: This field provides information on the cost of each item in the BOM. It can include the cost of raw materials, labor, overhead, and other indirect costs associated with the manufacturing process.
- Plant Data: This field specifies the location where each item in the BOM is stored, as well as the location where the finished product will be manufactured.
- Validity Date: This field specifies the period of time during which the BOM is valid. The validity date can be used to manage changes to the BOM over time.
In conclusion, the key components of the BOM in SAP Production Planning provide the information necessary to manage the production process effectively, ensure that the right materials and components are available when needed, and control the cost of manufacturing.
How does SAP Production Planning handle Material Requirement Planning (MRP)?
In SAP Production Planning, Material Requirement Planning (MRP) is handled using the MRP (Material Requirement Planning) module, which is part of the SAP ERP system. The MRP module helps to optimize production planning by considering current stock levels, planned and scheduled receipts, sales and production orders and other demands to calculate the precise material requirements and schedules.
MRP in SAP works based on the master data such as material master, bill of materials, and routing and transaction data like sales orders, production orders, stock levels, etc. It then uses various MRP algorithms to determine the net requirements for each material and creates planned orders or purchase requisitions to fulfill these requirements.
SAP MRP allows for various planning parameters like lot sizing, safety stock, lead time, and reorder point to be set for each material to ensure that material requirements are accurately planned. The results of the MRP run can be viewed and analyzed in various reports and list displays, and the planned orders can be converted into production or purchase orders with just a few clicks.
In short, SAP MRP helps companies to effectively plan and manage their material requirements to ensure that the right materials are available at the right time to support production, minimize stock-outs and optimize inventory levels.
What is Capacity Planning and how does it work in SAP Production Planning?
Capacity planning is the process of determining the production capacity of a company in order to meet future demand for its products. It involves analyzing the current capacity of the production facilities, machines, and workforce, as well as forecasting future demand and determining the necessary changes to meet that demand. The goal of capacity planning is to ensure that the company has the resources and production capabilities necessary to meet customer demand in a timely and efficient manner.
In SAP Production Planning, capacity planning is integrated into the production planning and scheduling process. The SAP Production Planning system uses information about the company’s production processes, workforce, and machinery to calculate capacity requirements for each production line. This information is then used to create a capacity plan for each production line and to determine the necessary changes to meet future demand.
SAP Production Planning also includes a capacity leveling tool that helps to balance capacity utilization across the production lines and ensure that the overall production process runs smoothly. This tool helps to identify areas where production bottlenecks may occur and to resolve these bottlenecks by re-scheduling work orders, adjusting production quantities, or adding additional resources.
In addition, SAP Production Planning includes a capacity requirements planning module that allows companies to plan and schedule production activities based on capacity requirements. This module allows companies to determine the production schedule that is most efficient and cost-effective based on the available resources and production capabilities.
In conclusion, capacity planning is an important component of production planning and scheduling, and SAP Production Planning provides a comprehensive and integrated solution for capacity planning. By ensuring that the company has the necessary resources and production capabilities to meet customer demand, capacity planning helps companies to improve efficiency, reduce costs, and increase customer satisfaction.
Can you explain the process flow for Shop Floor Control in SAP Production Planning?
Shop Floor Control in SAP Production Planning refers to the process of managing and controlling the production processes on the shop floor level. It ensures that the production processes are executed efficiently and effectively, and the production targets are met on time. The process flow of Shop Floor Control in SAP Production Planning involves the following steps:
- Master Data Creation: In this step, the master data required for Shop Floor Control is created, such as the Bill of Materials (BOM), routing, production version, and production order.
- Capacity Planning: In this step, the capacity requirements for each operation in the production process are determined, and the available capacity is evaluated.
- Production Order Creation: The production order is created based on the demand for the final product. The production order includes information on the material requirements, production targets, and production dates.
- Shop Floor Monitoring: The production process is monitored and controlled on the shop floor level. This includes updating the status of the production order, tracking the consumption of raw materials and production of semi-finished and finished products.
- Material Requirement Planning: This step involves the calculation of the material requirements based on the production order and the current stock levels.
- Goods Receipt: The goods receipt process involves receiving the finished products from the production process and updating the stock levels in the SAP system.
- Quality Management: This step involves the quality inspection of the finished products and the recording of any deviations from the quality standards.
- Billing: In this step, the billing for the production order is processed, and the invoices are generated.
In conclusion, Shop Floor Control in SAP Production Planning is a crucial process that helps in managing and controlling the production processes and ensuring that the production targets are met. The process flow involves the creation of master data, capacity planning, production order creation, shop floor monitoring, material requirement planning, goods receipt, quality management, and billing.
What is the role of Quality Management in SAP Production Planning and how does it work?
SAP Production Planning is a module that helps manage the production process, from demand forecasting and material requirements planning to production scheduling and capacity planning. Quality Management is an integral part of SAP Production Planning as it helps ensure that the products produced meet the required quality standards.
The role of Quality Management in SAP Production Planning can be summarized as follows:
- Quality Planning: It involves defining the quality standards that must be met for each product. This information is used to plan the quality control activities required to ensure that these standards are met.
- Quality Inspection: This involves performing inspection activities to ensure that the products being produced meet the required quality standards. The inspection activities can be performed in-process, at the end of the production process, or both.
- Quality Control: This involves using the results of the inspection activities to determine if the products produced meet the required quality standards. If the products do not meet the standards, corrective actions are taken to improve the quality of the products.
- Quality Reporting: This involves documenting and reporting the results of the quality control activities. The reports can be used to identify areas where quality improvements can be made, as well as to measure the effectiveness of the quality control processes.
Quality Management in SAP Production Planning works by integrating the quality management activities into the production planning process. The quality standards and inspection activities are defined in the system, and the results of the inspection activities are used to determine if the products produced meet the required standards. If the products do not meet the standards, corrective actions are taken to improve the quality of the products.
In conclusion, Quality Management plays a crucial role in SAP Production Planning as it helps ensure that the products produced meet the required quality standards, thus improving customer satisfaction and reducing the risk of product defects. The integration of quality management into the production planning process helps to ensure that quality control activities are performed in an efficient and effective manner, leading to improved quality and reduced costs.
How can you perform Backflush Processing in SAP Production Planning?
Backflush Processing in SAP Production Planning is a process that allows for the automatic posting of goods issues from the production order after a production confirmation is made. This process simplifies the manual effort required for material consumption postings and reduces the lead time for production accounting.
Here are the steps to perform Backflush Processing in SAP Production Planning:
- Configuration of Backflush Processing: Firstly, you need to configure the settings for Backflush Processing in SAP Production Planning. This is done in the customizing section of the SAP system by navigating to “SPRO” -> “Production Planning and Control” -> “Master Data” -> “Materials” -> “Define Backflush Processing”.
- Creation of Production Order: Create a Production Order in the SAP system using the transaction code “CO01”. This will be used to trigger the Backflush Processing during the confirmation process.
- Posting of Bill of Material: Next, you need to post the Bill of Material (BOM) of the finished product. This is done in the customizing section of the SAP system by navigating to “SPRO” -> “Production Planning and Control” -> “Master Data” -> “Materials” -> “Define Bill of Material”.
- Confirmation of the Production Order: After the BOM is posted, you can now perform a production confirmation using the transaction code “CO11N”. During this process, the system will automatically trigger the Backflush Processing and post the goods issue for the consumed materials.
- Monitoring of Backflush Processing: Finally, you can monitor the Backflush Processing results by navigating to the “Production Order” screen and checking the “Stock/Requirements List” tab. You can also check the “Materials Requirement Planning (MRP)” tab to see the updated availability of the consumed materials.
Note: It is important to ensure that the material master records for the consumed materials have the necessary settings for Backflush Processing before the process is performed.
What are the different types of Routing in SAP Production Planning and how do they work?
Routing in SAP Production Planning is the process of defining the steps and operations involved in the production of a finished product. There are four main types of routing in SAP Production Planning, including:
- Standard Routing: This is the most common type of routing in SAP Production Planning. It defines the standard sequence of operations for producing a specific material. The standard routing is used to calculate production times and costs and serves as a reference for other routings.
- Alternative Routing: Alternative routing is used when there is a need to change the standard routing due to a change in production process, technology, or material requirements. The alternative routing can be used to adjust the standard routing as per specific production requirements.
- Capacity Routing: Capacity routing is used to plan the production process and to ensure that the required resources are available to produce the material. It helps in determining the production capacities and times for each operation and machine.
- Task List Routing: Task list routing is used to define a detailed list of tasks and operations that need to be performed for a particular material. It is used to plan the production process and to ensure that the required resources are available.
In conclusion, the different types of routing in SAP Production Planning work by providing a clear and concise definition of the steps involved in producing a finished product. The routing information is used to plan the production process, calculate production times and costs, and ensure that the required resources are available.
Can you explain the process flow for Sales and Operations Planning in SAP Production Planning?
The SOP process in SAP Production Planning can be divided into the following steps:
- Data Collection: This step involves collecting data from various sources such as sales data, production data, and other relevant data. This data is then used to create a baseline for sales and operations planning.
- Demand Forecasting: In this step, the data collected is analyzed to predict the future demand for products. This is done using statistical methods and algorithms to create a forecast for the future demand.
- Capacity Planning: This step involves analyzing the production capacity of the organization and determining the resources that will be required to meet the demand forecast.
- Sales and Operations Planning: In this step, the demand forecast is compared to the production capacity, and the necessary adjustments are made to ensure that the production plan aligns with the sales plan.
- Production Planning: This step involves creating a detailed production plan based on the sales and operations plan. This plan includes the production schedule, resources required, and production quantities.
- Material Requirement Planning: This step involves determining the materials required to meet the production plan, including the quantity and timing of material purchases.
- Scheduling and Monitoring: This step involves monitoring the progress of the production plan and making any necessary adjustments to ensure that the plan is being executed effectively.
- Evaluation and Reporting: This step involves evaluating the results of the sales and operations planning process and creating reports to communicate the results to relevant stakeholders.
Overall, the Sales and Operations Planning process in SAP Production Planning is a continuous process that involves ongoing monitoring and adjustments to ensure that the production plan aligns with the sales plan and that the organization is able to meet the demand for its products.
How does SAP Production Planning support Lean Manufacturing and Industry 4.0?
SAP Production Planning supports Lean Manufacturing and Industry 4.0 by providing features such as:
- Real-time data and visibility: SAP PP provides real-time data and analytics, which helps manufacturers to make data-driven decisions and improve operational efficiency.
- Lean Manufacturing principles: SAP PP helps to reduce waste and improve process flow through Lean Manufacturing principles such as Value Stream Mapping, 5S, and Kaizen.
- Predictive Maintenance: SAP PP integrates predictive maintenance and machine learning algorithms, enabling predictive maintenance to minimize downtime and improve production efficiency.
- Automation: SAP PP provides an automated production planning and scheduling process that reduces manual intervention and errors.
- Connected Supply Chain: SAP PP connects all components of the supply chain, from raw material procurement to delivery of finished goods, ensuring seamless integration and collaboration.
- Smart Factory: SAP PP supports Industry 4.0 through the implementation of Smart Factory concepts such as smart sensors, machine learning, and IoT technology.
Can you explain the concept of Process Manufacturing in SAP Production Planning?
Process manufacturing in SAP Production Planning refers to the production of goods that undergo a sequence of steps, transformations, and chemical reactions to produce a final product. This type of production is common in industries such as food and beverage, chemical, and pharmaceuticals.
In SAP, process manufacturing is managed through the Process Order module, where a process order is created to define the production process, including the raw materials, inputs, and production steps. The system then generates a production batch, which is used to track the consumption of raw materials and the production of the final product.
Additionally, SAP provides features such as recipe management, where a set of instructions can be defined for the production process, and batch management, where batch-specific data can be recorded and tracked. These features help ensure consistent quality and reduce waste in the production process.
Overall, the SAP Production Planning solution for process manufacturing provides a comprehensive and integrated approach to managing production processes, enabling companies to streamline their operations and improve efficiency.
Basic Interview Questions
1. What exactly is SAP PP C_TS422_1909?
SAP PP process is related to a company’s production planning and includes all activities such as MRP (Material Requirement Planning), BOM (Bills Of Material), Routing, Capacity Planning, and so on, but it primarily consists of two segments.
- Material Planning entails the planning of material requirements as well as long-term planning.
- Planning for execution includes the creation of a production order, workflow, conformations, technical completion, and good movement.
2. Mention the SAP manufacturing process.
In SAP, there are three types of production processes.
- Manufacturing that is discrete
- Manufacturing That Is Repetitive
- Industries of Production and Processing
3. What activities are carried out in Production Planning?
Production Planning entails a variety of activities.
- master of material processing
- Making a Bill of Materials
- Work centre and routing are display.
- Keeping a planning calendar
- Next, Keeping the production lot
- Keeping a quota file
- Defining the coverage profile range and the profile for safety time
- Defining MRP perspectives
4. What do you understand by Routing in SAP PP C_TS422_1909?
In SAP PP, routing refers to a list of activities that must be complete in order to produce any material. When you estimate the cost of a material, for example, the system activates the relevant routing and activity rates for all those described in routing. This will be useful for calculating processing costs in product costing.
5. What are the steps involved in the Production Execution Process?
Steps in Production Execution include
- Firstly, Changing a planned order into a production order
- Secondly, The production order is being release.
- Next, Goods issued in response to a production order
- Further, Order confirmation for production
- Receipt of goods in accordance with the production order
6. What reports are generated by the product cost controlling information system?
The Product Cost Controlling Information System generates data for the areas listed below.
- Controlling the cost of the object with the subcomponents
- Next, Product cost by time
- Product cost based on order
- Further, Product cost base on sales order
- Intangible goods and services costs
- Material Ledger / Actual Costing
7. Explain what a “work centre” is in SAP PP and what data is used for in Work Centers.
“Work Centers” are SAP-PP business objects use in task list operations (routings, maintenance task lists, inspection plans) and work orders.
The data in the work center is used for:
- Scheduling: Formulas and operating time are entered to calculate the duration of an operation.
- Costing: Formulas are entered to calculate the costs of an operation.
- Capacity Planning: The available capacity and capacity requirement formulas are entered.
- Simplifying operation upkeep: The work centre can contain a variety of default values.
8. What are the benefits of MRP PP evaluations?
This role includes a function for evaluating the MRP outcome. This function can be use to locate information about material availability and to identify any material shortage situations.
9. Explain the purpose of using Capacity Planning.
Capacity Planning aids in all phases of planning:
- Planning for long-term rough cuts
- Long-term planning
- Planning for the short term
- It can be integrate with a variety of SAP applications, including SAP-SD, PP, PP-SOP, PP-LTP, PP-SFC, and others.
10. Describe how you can create a production order without routing and a BOM.
You can create a production order without a BOM or routing by changing the configuration in OPL8 (order type dependent parameters) to routing optional. When we attempt to create an order with C001, it may prompt us for a sales order.
11. What happens to planned once it is converted into a production order?
When a planned order is convert to production order, it is offset by the production order. The production order contains a reference to the planned order.
12. What is the difference between a stock transport order and a stock transfer order?
- Stock transfer order: It refers to the transfer of stock for use within the same company.
- Stock transport order: This refers to the transfer of ownership of stock in the buyer’s name.
13. What is PRT (Production Resource Tools) in SAP PP in C_TS422_1909 – SAP Production Planning and Manufacturing?
PRTs (Production Resource Tools) are moveable operating objects that are use to perform repetitive activities in plant or production maintenance, such as documents such as drawings or programs that use document management functions. Other PRT components include
- Engineering drawings
- Jigs, Fixtures, and Measurement Instruments
14. Can you explain how to make PRT master records?
The following steps must be taken in order to create PRT master records.
- Select logistics/accounting -> Project System -> Basic data -> Master data -> Production resources and tools Create
- The initial PRT creation screen appears.
- Enter a PRT number and click Continue.
- The primary data screen appears.
- Keep the basic information.
- Select Goto -> Defaults and fill in the default values.
- Keep the PRT.
15. What is the t-code for changing the production order and displaying the production order?
- C002 is the T-code for changing the production order.
- C003 is the T-code for displaying the production order.
16. Describe PLM (Product Lifecycle Management) in SAP PP and its application.
It is a collection of solutions that allow you to digitally create, maintain, and make product information available throughout the company and throughout the product’s life cycle.
PLM gives you the ability to do the following things:
- The workplace is an open portal on the internet that gives you access to all of the applications and information you need to collaborate with all external and internal business partners.
- It can communicate with other internet-base applications such as programme management, change and configuration management, and engineering collaboration.
17. What are the costing parameters in SAP-PP in C_TS422_1909 – SAP Production Planning and Manufacturing?
The costing parameters in SAP-PP are as follows.
- Work Centers: Activity Types and Formulas, Cost Centers
- Routing: The time, the types of activities
18. In the cost controlling information system, what fields are listed in the report’s list screen?
The following fields are listed in the report’s list screen:
- Key Figures
- Costing/MM
- %Costing/MM
- Revaluation
- VarCstRuns
- %VarCstRuns
- Basic data
- Valuation
- Cost component group 1/ Cost component group 2
- CostCompGr(fix) 1 / CostCompGr( fix) 2
19. Explain the purpose of SAP Material View and list other parameters where SAP Material View can be used.
SAP Material View is an SAP object that contains not only the name of the material but also various other material-related information.
- Firstly, Information on material production
- Secondly, Information on material planning
- Next, Information on material sales
- Information on material purchases
- Information on material storage and warehousing
- Accounting and material costing information
- Material batch specification data
20. Describe the various types of Master Views for Production and Planning.
Master Views are used for production and planning:
- Firstly, SAP MRP1 View
- Next, SAP MRP2 View
- Further, SAP MRP3 View
- SAP MRP4 View
- SAP Work Scheduling View
21. What are the different types of MRP (Material Requirement Planning)?
MRP types are divided into two leagues.
- Consumption-based planning materials
- Demand-driven planning
22. Describe the keyfields found in MRP View 1 in C_TS422_1909 – SAP Production Planning and Manufacturing.
MRP views 1 are mostly kept around for production.
- General Information
- MRP Procedure Data on Lot Size
23. Could you please describe the basic procedure for dispatching operations in capacity leveling?
The basic procedure for dispatch operations is as follows:
- Firstly, The dispatch date is either determine by the user or specified by scheduling.
- Secondly, If several operations must be dispatched, a dispatching sequence must be determine.
- Next, The dates when operations will be dispatch
- Also, The work center to which operations will be route
- Next, Finite scheduling is carried out.
- The operation is checked.
- Further, The operation’s status is set to “dispatched.”
- The system performs midpoint scheduling.
24. Explain why an MRP list is required if the stock requirement list is already provided.
The MRP list displays the outcome of the most recent planning run; changes that occurred between planning runs are ignore. In contrast, the system displays all changes that occurred in the stock, issues and receipts in the stock or requirement list.
25. Describe the t-codes for creating, changing, and summarising BOM.
BOM transaction codes for:
- Creating BOM= CS01
- Changing BOM= CS02
- Summarized BOM=CS13
26. Explain the function of t-code CS20 in BOM.
With t-code CS20, you can make mass changes to the BOM, such as:
- Firstly, modify the item data
- Secondly, creating new content
- It is being replaced with another material.
27. What is Backflush, and where does it come into play?
Backflushing is nothing more than a mechanical goods issue. When you confirm the operations, the system will automatically post the goods issue. There is no need to create a manual issue. It will reduce the amount of effort required. Backflushing is the automatic accounting (Goods issues – 261 mvt) of production material consumed at the time of confirmation. For example, when a four-wheeler vehicle is rolled off the assembly line, the four wheels and tires are deemed to be consume and automatically issue to the production order by the system via backflushing.
28. Define Planning time Fence in C_TS422_1909 – SAP Production Planning and Manufacturing.
Time management planning. The planning time fence specifies a period during which no automatic changes to the master plan are to be made. Workdays are use to keep the planning time fence in place. It is only use for materials planned with an MRP type that includes a firming type.
29. What do you understand by time-phased Planning?
Time-Phased planning, in technical terms, postpones the release of procurement proposals for components until they are actually required, and offsets the requirements by the lead time involve.
30. Explain Phantom Assembly in C_TS422_1909 – SAP Production Planning and Manufacturing.
Phantom assemblies are assemblies that have their own product structure but do not actually exist physically. The phantom assembly’s components are directly incorporate into the superordinate product. The superordinate product’s product structure includes a reference to the phantom assembly. In the same product structure, a phantom assembly can be referenced multiple times. Changes are immediately visible and effective in all usage locations.