C_TS422_2020 SAP Production Planning and Manufacturing Interview Questions
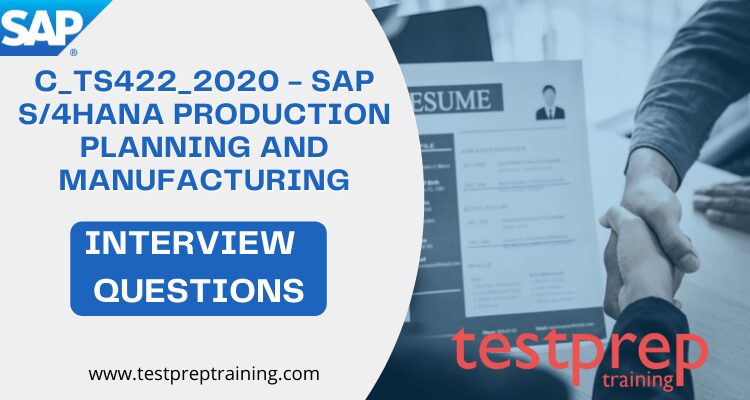
The C_TS422_2020 SAP S/4HANA Production Planning and Manufacturing (PP&M) is the centralized platform for all production planning and manufacturing activities throughout an enterprise. So, if you want a career creating exciting new products without constraints, you must pass the interview round. To pass the interview, you must be able to demonstrate the skills and competencies needed for the C_TS422_2020 SAP S/4HANA Production Planning and Manufacturing consultant position. You must possess a good overall understanding of the implementation process and different planning techniques, and must be able to put that knowledge into practice.
Because job interviewers often ask similar questions, you will be better prepared to handle such queries if you are familiar with some of the most common topics that are brought up in the C_TS422_2020 SAP S/4HANA interviews. Here is a list of some highly expected C_TS422_2020 SAP S/4HANA interview questions!

What is SAP PP and what are its main features?
SAP PP (Production Planning and Manufacturing) is a module within the SAP ERP system that provides a comprehensive solution for production planning, control, and execution. Its main features include:
- Material Requirements Planning (MRP): Automates the calculation of material requirements based on production plans, sales orders, and other data.
- Capacity Planning and Scheduling: Supports the planning and scheduling of production activities, including resource planning and load balancing.
- Production Planning and Control: Facilitates the planning, execution, and control of production processes.
- Shop Floor Control: Provides real-time data and visibility into production operations, including machine utilization, operator efficiency, and production performance.
- Bill of Material (BOM) Management: Allows the definition and maintenance of complex bills of material and their associated costs.
- Goods Receipt and Goods Issue: Manages the physical movement of materials and products into and out of production processes.
- Work Centers and Routing: Defines the work centers, operations, and sequence of activities required for production.
- Repetitive and Process Manufacturing: Supports both repetitive and process manufacturing, including batch and continuous production processes.
These features, among others, make SAP PP an essential tool for organizations looking to optimize their production and supply chain management processes.Regenerate response
How does SAP PP integrate with other modules in the SAP ERP system?
SAP PP integrates with several other modules in the SAP ERP system to provide a comprehensive solution for production planning and control. Some of the key integrations include:
- SAP Material Management (MM): SAP PP integrates with MM to manage material requirements, including the calculation of material requirements, goods receipt, and goods issue.
- SAP Sales and Distribution (SD): SAP PP integrates with SD to provide real-time visibility into sales orders, delivery schedules, and other customer-related data.
- SAP Quality Management (QM): SAP PP integrates with QM to support quality control and inspection during production processes.
- SAP Financial Accounting (FI): SAP PP integrates with FI to manage financial data related to production, including cost centers, cost categories, and cost elements.
- SAP Plant Maintenance (PM): SAP PP integrates with PM to manage the maintenance and utilization of production resources, such as machines and work centers.
- SAP Warehouse Management (WM): SAP PP integrates with WM to manage the physical storage and movement of materials and products within the warehouse.
These integrations allow organizations to manage production and supply chain processes in a seamless and integrated manner, reducing the risk of errors and improving efficiency. The integration also enables real-time data exchange between modules, making it easier for organizations to make informed decisions about production and supply chain management.Regenerate response
Can you explain the process of material requirements planning (MRP) in SAP PP?
Material Requirements Planning (MRP) is a critical component of the SAP PP (Production Planning and Manufacturing) module. The MRP process in SAP PP involves the following steps:
- Data Collection: The first step in the MRP process is to collect data from various sources, including sales orders, delivery schedules, production plans, and inventory levels.
- Calculation of Material Requirements: Based on the collected data, SAP PP calculates the material requirements for each product, taking into account the lead time, safety stock, and lot sizing rules.
- Generation of Purchase Requisitions: If the material requirements cannot be met from the existing inventory, SAP PP generates purchase requisitions to purchase the required materials from suppliers.
- Availability Check: SAP PP performs an availability check to determine if the materials are available in the warehouse or if they need to be procured.
- Rescheduling: If the required materials are not available, SAP PP reschedules the production plan to take into account the new delivery schedule for the materials.
- Re-calculation of Material Requirements: If the production plan is rescheduled, SAP PP recalculates the material requirements to ensure that the new plan is feasible.
- Generation of Production Orders: Based on the final material requirements, SAP PP generates production orders to start the production process.
The MRP process in SAP PP is dynamic and iterative, allowing organizations to respond to changes in demand, supply, and other factors in real-time. The process helps organizations to ensure that they have the right materials, in the right quantities, at the right time to meet production and customer needs.Regenerate response
How does SAP PP handle capacity planning and scheduling?
SAP PP handles capacity planning and scheduling by providing a range of tools and functions to plan and optimize the utilization of production resources, such as machines and work centers. The key features and processes used for capacity planning and scheduling in SAP PP include:
- Work Center Definition: Work centers are defined in SAP PP to represent the production resources in an organization, including machines, people, and tools. The work center definition includes information such as capacity, availability, and utilization.
- Capacity Planning: SAP PP provides a capacity planning function that allows organizations to plan and allocate production resources based on the demands of the production plan. The capacity planning function takes into account factors such as machine utilization, maintenance schedules, and downtime to ensure that the production plan is feasible.
- Scheduling: SAP PP provides a scheduling function that allows organizations to schedule the production plan based on the availability of production resources. The scheduling function takes into account the production lead time, production quantities, and production dependencies to create a feasible and optimized production schedule.
- Simulation: SAP PP provides a simulation function that allows organizations to test different production scenarios and make adjustments to the production plan based on the results of the simulation. The simulation function provides a visual representation of the production plan and allows organizations to evaluate different options and make informed decisions.
These features and processes allow organizations to effectively manage the utilization of production resources, reduce production lead time, and optimize production costs. By using SAP PP for capacity planning and scheduling, organizations can improve the efficiency of their production processes and ensure that they meet customer demands and business goals.
Can you explain the difference between the make-to-stock and make-to-order production scenarios in SAP PP?
Make-to-Stock (MTS) and Make-to-Order (MTO) are two common production scenarios in SAP PP (Production Planning and Manufacturing) that determine how a company produces and delivers products to customers.
Make-to-Stock (MTS): In a Make-to-Stock scenario, a company produces and stocks products based on an estimated demand, without a specific customer order. This production scenario is typically used for products that have a high demand and predictable sales, such as fast-moving consumer goods. In an MTS scenario, the production process is initiated based on a forecast of future demand, and the resulting products are held in inventory until a customer order is received.
Make-to-Order (MTO): In a Make-to-Order scenario, a company produces products only after a specific customer order is received. This production scenario is typically used for products that have a low demand or are customized for each customer, such as special-order products or products with high customization options. In an MTO scenario, the production process is initiated only after a customer order is received, and the resulting product is delivered directly to the customer.
In SAP PP, the production scenario is defined at the material level and can be changed as needed to support different production processes. The choice between MTS and MTO will depend on the type of product being produced, the level of customization required, and the level of inventory risk the company is willing to take. By choosing the appropriate production scenario, companies can ensure that they are producing the right products, in the right quantities, at the right time to meet customer demand and business goals.
How does SAP PP support shop floor control and production execution?
SAP PP (Production Planning and Manufacturing) supports shop floor control and production execution through the following features and processes:
- Production Order Management: SAP PP provides a production order management process that allows organizations to plan, release, and execute production orders for the manufacture of products. The production order includes information such as the product to be produced, the production quantities, and the production routing, which defines the operations required to manufacture the product.
- Shop Floor Control: SAP PP provides a shop floor control function that allows organizations to manage the execution of production orders on the shop floor. The shop floor control function provides real-time information on the status of production orders, including the progress of each operation, the status of production resources, and the status of materials and components.
- Production Confirmations: SAP PP provides a production confirmation process that allows organizations to record the actual quantities of materials and components used and the actual production times for each operation in the production process. The production confirmations are used to update the production order status and to provide accurate cost and performance data for production analysis.
- Material Availability Check: SAP PP provides a material availability check function that ensures that the necessary materials and components are available before the production order is released for execution. The material availability check function takes into account the current inventory levels, the status of purchase orders and production orders, and the production lead time to ensure that the necessary materials are available when needed.
What is the use of bills of material (BOM) in SAP PP and how are they maintained?
Bills of Material (BOM) play an important role in SAP PP (Production Planning and Manufacturing) by providing the detailed information required to manufacture a product. A BOM is a list of all the components and materials required to manufacture a product, including the quantities of each component required for each unit of the product.
The following are the main uses of BOMs in SAP PP:
- Production Planning: BOMs are used in SAP PP to plan and execute the production of products. The BOM provides information on the components and materials required to manufacture a product, as well as the quantities of each component required. This information is used to plan the production process, including the ordering of materials and components, the scheduling of production operations, and the assignment of production resources.
- Costing: BOMs are used in SAP PP to calculate the cost of each product. The BOM provides information on the components and materials required to manufacture a product, as well as the quantities of each component required. The cost of each component and material is used to calculate the cost of each product, including the direct and indirect costs associated with the production process.
BOMs in SAP PP are maintained in the system using the BOM maintenance transactions. The BOM maintenance transactions allow users to create and maintain the BOM structure, including the definition of the components and materials required to manufacture a product and the quantities of each component required. BOMs can be maintained at the header material level or at the sub-item level, depending on the level of detail required.
Can you describe the process of goods receipt and goods issue in SAP PP?
Goods receipt and goods issue are two key processes in SAP PP (Production Planning and Manufacturing) that are used to manage the flow of materials and components in and out of the production process.
Goods Receipt: The goods receipt process in SAP PP is used to record the receipt of materials and components into the production process. This process involves the following steps:
- Purchase Order (PO) Creation: A purchase order is created in SAP PP to request the delivery of materials and components from suppliers. The PO contains information on the items being purchased, the quantities being ordered, and the delivery date.
- Goods Receipt Notification (GRN): The supplier sends a goods receipt notification to the company to confirm the receipt of the materials and components. The GRN contains information on the items received, the quantities received, and the delivery date.
Goods Issue: The goods issue process in SAP PP is used to record the consumption of materials and components during the production process. This process involves the following steps:
- Material Requirements Planning (MRP): The MRP process in SAP PP is used to calculate the quantities of materials and components required to meet the production requirements. The MRP process considers the inventory levels of materials and components, the production schedule, and the lead times for procurement.
- Reservations: Reservations are created in SAP PP to reserve the required quantities of materials and components for specific production orders. The reservations are used to ensure that the materials and components are available for the production process and to prevent over-allocation.
What is the role of work centers and routing in SAP PP?
Work Centers and Routing are two important concepts in SAP PP (Production Planning and Manufacturing) that are used to define and manage the production process.
Work Centers: A work center in SAP PP is a resource that is used to perform a specific operation in the production process. Also, work centers can be physical locations, such as a machine or a workshop, or they can be virtual resources, such as a team of workers. Further, work centers are defined in the system with information on their capacity, availability, and performance.
Routing: A routing in SAP PP is a sequence of operations that are required to produce a specific product. The routing defines the work centers that are required to perform the operations, the sequence in which the operations are performed, and the setup and run times for each operation. The routing is used to determine the production time and the resource requirements for each product.
The role of work centers and routing in SAP PP is to provide a clear and accurate definition of the production process. By using work centers and routing, organizations can plan their production processes more effectively, ensuring that they have the resources and capacity to meet the production requirements. They can also use the work centers and routing information to calculate the costs of production and to monitor the performance of their production processes.
By accurately defining the production process with work centers and routing, organizations can improve their production planning and control, leading to better delivery times, lower costs, and higher quality products.
Can you explain the difference between repetitive and process manufacturing in SAP PP?
Repetitive and process manufacturing are two different production processes that can be managed in SAP PP (Production Planning and Manufacturing).
Repetitive Manufacturing: Repetitive manufacturing is a production process where a large number of identical items are produced continuously in a repeating cycle. In this type of production process, the production process is well defined and standardized, and the production schedule is based on a set production rate. Repetitive manufacturing is typically used in industries such as automotive, electronics, and aerospace.
Process Manufacturing: Process manufacturing is a production process where a large number of different items are produced in a batch process. In this type of production process, the production process is more flexible and can vary based on the specific requirements of each batch. Process manufacturing is typically used in industries such as chemicals, pharmaceuticals, and food and beverage.
The main difference between repetitive and process manufacturing is the degree of flexibility and standardization in the production process. In repetitive manufacturing, the production process is well defined and standardized, while in process manufacturing, the production process is more flexible and can vary based on the specific requirements of each batch.
SAP PP provides support for both repetitive and process manufacturing, allowing organizations to manage their production processes more effectively. By using SAP PP, organizations can improve their production planning and control, leading to better delivery times, lower costs, and higher quality products.

1. Can you explain what is meant by advance planning in SAP?
SAP Advanced Planning and Optimization offers a range of functions that help organizations coordinate supply chain activities across all stages. This allows for the performance of partner interactions as well as supplier contract management.
2. In which SAP S/4HANA features have advanced capabilities been embedded?
SAP APO (Advanced Planning and Optimization) is now SAP IBP (Integrated Business Planning) and S/4HANA (Business suite 4).
3. What do you know about alert monitoring?
Alerting is the part of a monitoring system that notifies people when things go wrong. If you set an alert for the value of a metric, you can be notified if the values fall outside of the acceptable range. Alerts are composed of two parts: conditions and actions.
4. How would you explain what is detailed scheduling?
Production scheduling is a complex process that optimizes the use of resources to meet schedule requirements. It takes into consideration resource and material availability. The objective is for the production planning to be completed in a timely manner, with the appropriate level of quality.
5. Is production planning and detail scheduling available in SAP ECC?
In SAP S/4HANA, production planning (now part of APO) is integrated into the same application as material requirements planning and capacity planning.
6. How do you confirm a Production Order?
To confirm a Production Order, enter T-code CO15. Next, enter the order number and click the tick mark button. The new window will ask you to confirm the production quantity to be declared.
7. Do you know why the production version is mandatory in S/4 Hana?
For manufacturing, only production versions are valid sources of supply in SAP S/4HANA. Production versions make sourcing more similar to MRP and PP/DS. This similarity between sourcing and production versions means that MRP and PP/DS, as they’re both run in production, are more alike in SAP S/4HANA than they would be if you run them with no production version at all.
8. Can you tell if the MRP area is mandatory?
Materials management can be managed by different materials requirements planning (MRP) controllers, depending on where the materials are located. Materials locations are handled by materials requirements planning (MRP) areas in SAP S/4HANA. These MRP areas are obligatory and have replaced storage location MRP.
9. Can you define what an order status is?
In contrast to general SAP status management, the system status does not have a function in order management. The status of an order is directly linked to it, so it is automatically changed when the status changes.
10. As an SAP S/4HANA (C_TS422_2020) associate what is your understanding of the availability check in SAP?
The availability check (or ATP check) involves checking whether a product is available in a sales order. The system reserves the product in the required quantity, and the system transfers the ATP requirements to production or purchasing.
11. How would you describe master data in S/4HANA?
Master data management is a collaboration between IT and business stakeholders to ensure that the enterprise’s official shared master data assets are uniform, accurate, stewarded, consistent, and accountable.
12. What is SAP product master data?
Product master data consists of the details needed to plan, support logistics and forecasting processes, and prepare financial statements. For example, product master data is referenced when you are planning promotions or scheduling demand modeling and forecasting processes.
13. Can you distinguish between product and material in SAP?
Material is a tangible product, for example, packaging, auxiliary materials, and expendable supplies. While a product is a commodity that serves as the object of the business of a company and creates value for this company.
14. What do you understand by material requirement planning?
In SAP’s Enterprise Resource Planning (ERP) software, the Material Requirements Planning (MRP) module serves as a planning tool that helps production and procurement planners create feasible and realistic plans so the process of procuring or producing can proceed quickly.
15. Who would be held responsible for material requirements planning?
The MRP controller is responsible for assisting with planning the production of both finished goods and raw materials by monitoring material requirements, generating production orders, and placing purchasing orders.
16. What are the techniques of materials planning?
Methods that are most prevalent and used are:
- Re-order point systems
- Run-out time planning
- Material requirements planning (MRP)
- Kanban and order-based planning (OBP)
17. What is the lot size in SAP?
The lot size is the maximum quantity of goods that are to be create in a production order or purchase order. This prevents orders from being create in non-economic quantities and allows the company to streamline its manufacturing process.
18. Could you tell me something about SAP lean manufacturing?
SAP ERP – Lean Manufacturing – Planning & Control is an automotive consulting solution that offers a complete integrated solution for lean manufacturing. It offers an enhanced planning cockpit, a leveling (Heijunka) function, and the ability to use production schedules/rhythm wheels.
19. As an SAP S/4HANA (C_TS422_2020) associate what do you know about repetitive manufacturing processes?
Repetitive manufacturing is the production of products in rapid succession. It is useful to manufacturers who maintain a steady supply of one or more kinds of products over a long period. Such manufacturing can be use for mass production by both discrete and process manufacturers.
20. How would you describe what load planning is?
Load planning, a method of consolidating cargo to maximize the capacity of each vehicle and truck, can be used to reduce the number of vehicles needed for a shipment. The less time a vehicle spends in transit, the less likely it is to break down.
21. Can you explain SAP capacity planning and its types?
People use capacity planning to balance workloads at their work centers. You can calculate production capacity based on the products’ requirements and your available capacity. A planning table helps you plan for future workloads over time. It has three main types:
- Product capacity planning
- Workforce capacity planning
- Tool capacity planning.
22. What according to you is SAP Demand Management, in a nutshell?
Demand management is a key function of planners. Planners must anticipate how much customers need and make sure that those materials are available when needed. Demand management mainly focuses on forecasting customer requirements and balancing customer orders with production schedules.
23. What is the main point of difference between make to stock and make to order?
In simple terms, make-to-order production rates reflect actual orders while make-to-stock production rates are based on sales forecasts or predictions.
24. Could you distinguish between consumption-based planning and MRP?
MRP uses the inventory on hand, any expect receipts, and the requirements for sales orders or production orders to calculate how much material is need. In consumption-based planning, once a certain level of inventory is reach, it triggers the system to reorder more of that product.
25. What are the 5 steps to production planning?
- 1st step: forecasting the demand for the product.
- 2nd: determining the potential options for production.
- 3rd: choosing that production option that effectively uses a combination of resources
- 4th: monitoring and controlling
- 5th: Adjusting
26. Which supply chain management features are available in SAP S/4HANA Cloud?
- Consolidating the shipping processes for both inbound and outbound shipments.
- Streamlining the material flows and also reducing logistics costs.
- Defining comprehensive freight agreements involving complex calculation rules and performing accurate freight costing.
27. Could you elucidate on the SAP User Experience strategy?
The SAP User Experience (UX) strategy is aim at providing and maintaining great offerings to our consumers. Consumer software trends can influence the way consumers and employees expect to interact with enterprise products, so it is necessary for SAP’s UX strategy to meet these expectations.
28. Do you know what is the process order?
The process order is a document covering the manufacturing of goods and the rendering of services. It enables companies to plan their resources, control process order management, settle accounts according to contractual agreements, and maintain an orderly record of work done.
29. Can you explain the importance of GMP?
Manufacturers aim to execute consistent procedures within safe environments. Hence, they prevent contamination, recalls, and loss of profit. GMP protocols that lessen the risk of errors are strict, and they come with safeguards to protect the consumer and the bottom line. This can be accomplish by developing efficient systems and processes.
30. What motivated SAP S/4HANA enterprise management development?
SAP’s software was driving the demand for new capabilities among customers. Customers were looking for advanced planning and process optimization and improved data storage, along with better mobility and delivery of services across all of their devices.