C_TS450_1909 – SAP Certified Application Associate Interview Questions
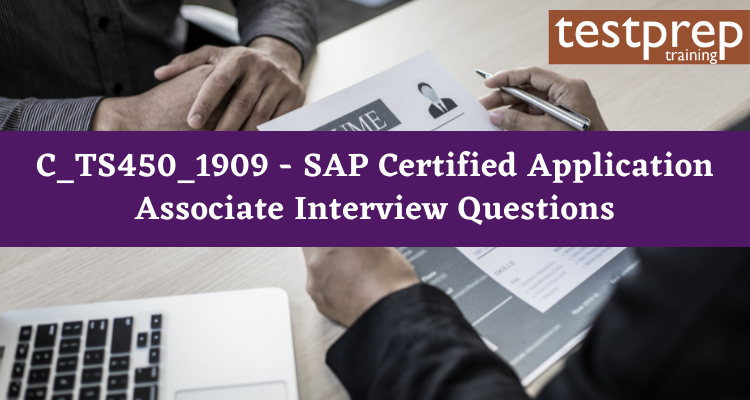
C_TS450_1909 – SAP Certified Application Associate The Sourcing and Procurement – Upskilling for ERP Experts have basic and core sourcing and procurement expertise, which is required for the consultant role. You need to have a thorough understanding of the material and the capacity to apply it to projects in order to contribute to the planning and implementation phases’ success in a mentoring position. In an interview for a C_TS450_1909 – SAP Certified Application Associate position, you demonstrate your expertise and ability in a certain sector or area by answering questions. You can prepare for a C_TS450_1909 – SAP Certified Application Associate interview by reviewing questions to get an idea of how to appropriately answer them. We’ve put together a list of frequently asked C_TS450_1909 – SAP Certified Application Associate interview questions, as well as some sample responses.
1. In C_TS450_1909, explain the sales process and analytics.
The process of detecting, modeling, understanding, and projecting sales patterns and results, as well as assisting in the understanding and identification of improvement points, is known as sales analytics. It’s used to evaluate the success of a prior sales campaign and predict how future campaigns will perform.
2. What is the role of the sales document type in the sales process?
Based on the sales document type, item type, and item category, the system replicates and controls advertising sales. The kind of sales document is specified during the development of a sales document.
3. How does the Billing Process Work?
In the SAP Sales and Distribution module, billing is the final step in the process of completing business transactions. When an order is processed and delivered, billing information is provided at each stage of the order processing process.
4. Specify the shipping procedure.
5. What is the notion of availability checks and how does SAP implement them?
There are three types of availability checks available:
- Carry out a check based on the ATP quantities.
- Ascertain that the product distribution is right.
- Compare the plan to the actual situation.
- You can choose whether an availability check should be performed against the ATP quantity or against planned in Customizing. The material master, as well as the rest of the system, manages the check against product allocations.
6. What exactly do you mean when you say “product allocation”?
Product allocation provides for the time-based delivery of products to certain clients or regions. As of Release 3.0F, you can now check availability against product allocation. If the output is low, for example, the first customer will not receive the whole amount, resulting in subsequent sales orders not being confirmed or being confirmed far too late.
7. Describe the requirements Class.
The requirements class contains all planning control elements, such as relevance for planning, requirements planning strategy, and requirements consumption strategy. Furthermore, whether an availability check for the material in the sales and distribution documents should be based on the ATP quantity (ATP = available to promise) and whether needs should be passed on are stated at the global level. For sales documents, the schedule line category gives a finer level of control.
8. Can you explain what the Checking group is all about?
The group in charge of checking determines whether the system should create individual or group sales and shipment processing needs. Here you can also set a material block for the availability check with requirement transfer. The checking group can also be used to disable the availability check. This option was created expressly for the assembly order so that when the bill of materials is detonated in the assembly order, the individual components can be designated as non-critical parts for procurement purposes. The availability check’s scope is defined by the checking group in conjunction with the checking rule.
9. Describe the checking rule in detail.
The checking rule is used in sales and distribution to regulate the scope of the availability check for each transaction. You can also choose whether to include or remove the replenishment lead time from the check. Individual checking criteria indicate which stock and inward and outward movement of commodities should be taken into account for the transaction-based availability check.
10. What are the components of the Check?
A checking rule is assigned to each transaction. This rule, in conjunction with the checking group, determines the scope of the availability check. You can select which of the elements described above should be included in the availability check for each transaction using the checking rules in Customizing for Sales.
In the availability check for-trade items, it makes no sense to include scheduled or production orders, for example. These orders should, however, be included in the check if your organization creates the products.
For transactions that generate special stock, such as make-to-order manufacture, consignment, or returnable packing processing, the availability check is done against the special stock.
11. What factors go into determining the pricing procedure?
Sales Area (Sales Organization + Distribution Center + Division) + Customer Pricing Procedure + Document Pricing Procedure determine the pricing procedure in SD. The Sales Area is provided at the Header Level of the Sales Order. The Customer Master is the foundation for the Customer Pricing Procedure. The Document Pricing Procedure is determined by the Sales Document Type / Billing Type (if configured). Once the pricing procedure has been determined, condition records are retrieved. If appropriate condition data are discovered, the price is established. The system will issue an error message if the Mandatory pricing criterion is not met.
12. In C_TS450_1909, explain Inbound Delivery Processing.
The process of obtaining items from a vendor that is triggered by an incoming delivery request is known as inbound delivery processing. It incorporates all aspects of the inbound delivery process (preparation and execution triggering), as well as vendor communication and billing.
13. What is the outbound delivery procedure?
The process of shipping items to a product recipient that is initiated by an outward delivery request is known as outbound delivery processing. It combines all outbound delivery-related operations (preparation and execution triggering), as well as contact with the goods received and invoicing.
14. In C_TS450_1909, explain Material Determination.
Within a given date range/interval, material determination replaces/exchanges one material in a sales order with another. When the condition is met, it employs the condition approach to swap out one material for another from the condition records.
Substitution can occur in a number of circumstances, including:
- Internal material is being used to replace customer stuff.
- Substituting new materials for obsolete ones
- Replace original material with supplied material during special offer periods.
15. What exactly do you mean when you say “site logistics processing”?
On-site logistics process planning, execution, and confirmation. Logistics procedures based on on-site logistics process models include picking, packaging, shipping, receiving, and value-added services.
16. In C_TS450_1909, define Dock Appointment.
For a specified amount of time, a reservation for a certain handling resource (a door) within a warehouse or yard.
17. Explain the Appointment of the Transportation Unit.
A Transportation Unit (TU) Appointment is a persistent object that holds a reservation for a certain physical transportation unit resource for a set amount of time. Firstly, the TU appointment also contains a set of statuses (such as checked-in, loading began, and so on) as well as actions that may be performed on it (post-check-in, etc.). The TU appointment allows for the planning and implementation of yard processes. The TU appointment is further divided into four categories: planned, active, executed, and invalidated. For each physical TU resource, there can only be one TU appointment with the state: active (when the physical vehicle actually is in the yard). The start and end time slots, as well as the executed start and end time points, are specified in the TU appointment.
18. In C_TS450_1909 , define Vehicle Appointment.
A vehicle appointment is a persistent object that stores a physical car resource for a certain amount of time. The vehicle appointment also includes a set of states (such as “Checked In,” “Loading Started,” and so on) and actions (such as “Post Check-In,” and so on) that can be performed on it.
19. How are partner functions used in sales?
In a commercial transaction, use partner functions to specify each business partner’s rights and duties. You assign partner functions when you establish a master record for a business partner.
20. What distinguishes partner functions?
Examples of partner functions defined in the standard system are as follows:
- Partner functions for client types that are partners
- Data on sales, such as the assignment to a sales office or a legitimate price list, is stored in the Sold-to Party field.
- Data for shipping, such as unloading point and products receiving hours, is stored in the Ship-to Party field.
- The address of the bill-to-party is included, as well as information on document printing and electronic communication.
- Payer is a database that stores information on billing schedules and bank account numbers.
- Vendors of the partner type have partner functions.
- Address for placing an order
- Goods supplier’s invoice is displayed.
- Payee alternative
- Other partner categories, such as personnel, have partner functions (HR master records)
- Employee in charge
- You can use this partner function to assign a buyer from your firm to a vendor, for example.
21. In C_TS450_1909 , what is the objective of batch management?
In numerous industries, particularly the process industry, you must work with homogeneous partial quantities of a material or product throughout the logistical quantity and value chain.
This is due to a number of factors, including:
- GMP (Good Manufacturing Practice) guidelines or hazardous material rules are examples of legal requirements.
- The necessity for regression, defect tracking, and callback activities
- The need for differential quantity- and value-based inventory management (for example, as a result of variable elements in Production or diverse yield/outcome characteristics).
- Production or procedural specifications Production or procedural specifications Differences in usage and their monitoring in SD and Production materials planning (for example, settlement of material quantities on the basis of different batch specifications).
22. What is Batch Status Management and why do we utilise it?
This component is used to determine whether a batch is useable or not. This allows you to stop goods from moving, as well as their delivery to customers and use in manufacturing, for unusable batches. You can highlight the differences between the two statuses in greater detail by using extra features that you’ve altered to match your needs. As a result, you can indicate the sort of usage for which a batch has been released or has not been released.
23. What are the advantages of using the Sales Order Fulfillment Cockpit?
The sales order fulfillment cockpit in SAP S/4HANA delivers the following business benefits:
- For starters, it provides visibility into order fulfillment.
- Second, it permits internal sales reps to concentrate on pressing concerns or unusual situations.
- Internal sales staff can take actions directly and track success at any moment by combining analytical insights and operational actions.
- Collaboration with internal and external contacts to solve problems is improved.
24. In C_TS450_1909 , define Collective Processing.
The Collective processing function shows you a list of all the transactions you’ve selected depending on the criteria you set on the first screen. By displaying a list of all transactions with common selection criteria and providing the appropriate processing capabilities, this tool streamlines transaction management. You can go straight from the processing list to the individual transaction to see more details. To speed up the selection and processing of all financial transactions, collective processing might be used. You can also use the collective processing mechanism to complete all necessary activities (such as knock-in or knock-out, exercise, or rollover).
25. In C_TS450_1909 , define the Manage Scheduling Agreement.
Users can view and display all scheduling agreements based on the criteria they set in the Manage Scheduling Agreement SAP Fiori app, as well as dive down into the specifics and make revisions and follow-up activities.
26. What are the components of revenue accounting and credit management?
SAP Credit Management (FIN-FSCM-CR) replaces SD credit management in SAP S/4HANA. SAP offers migration options for SAP Credit Management, which contain the following elements:
- To begin, there is information about configuration.
- Second, master data is essential.
- Information about credit risk
- Information about credit decisions
- In revenue accounting, SAP Revenue Accounting and Reporting replaces SD revenue recognition. SD revenue recognition is not supported by SAP S/4HANA. Instead, SAP S/4HANA functionality should be used, which supports the new revenue accounting standard based on International Financial Reporting Standard 15 (IFRS 15) and local generally accepted accounting standards (GAAPs).
27. What distinguishes C_TS450_1909 ‘s Transaction Management?
Entering and processing financial transactions for the following product categories is part of transaction management:
- Fixed-term deposits and notice deposits
- Second, there is Commercial Paper.
- Finally, there are cash flow transactions.
- Then there are interest rate instruments.
- In addition, Facilities
- Further, Transactions in spot and forward exchange
- Derivatives of interest rates
- Option types include over-the-counter (OTC) and listed options.
- Futures
- Security transactions are also included.
- Assurance Letters of Credit
28. What distinguishes Time Deposit – Fast Processing from other deposit options?
You can use the fast-processing feature to pick and process fixed-term and notice deposits for numerous company codes in one go. Only a few key fields are available for this function. It helps you save time by allowing you to complete the majority of your everyday duties from a single entry screen. For regular entry, you can alternatively go to the detail screen.
29. How does Securities Lending help?
Use this function if you wish to manage and update many lending transactions at the same time. Lending transactions can be filtered based on your chosen criteria and displayed in a list with a brief summary. You can also change or view comprehensive information about individual transactions by navigating from the processing list to the individual transactions.
30. What is the purpose of C_TS450_1909 ‘s Availability Check?
The system assesses whether a product may be confirmed as available in a sales order when it performs an availability check (ATP check) (enough stock is available or can be produced or purchased on time). The product is reserved in the needed quantity, and the ATP requirements are passed on to production or purchasing.